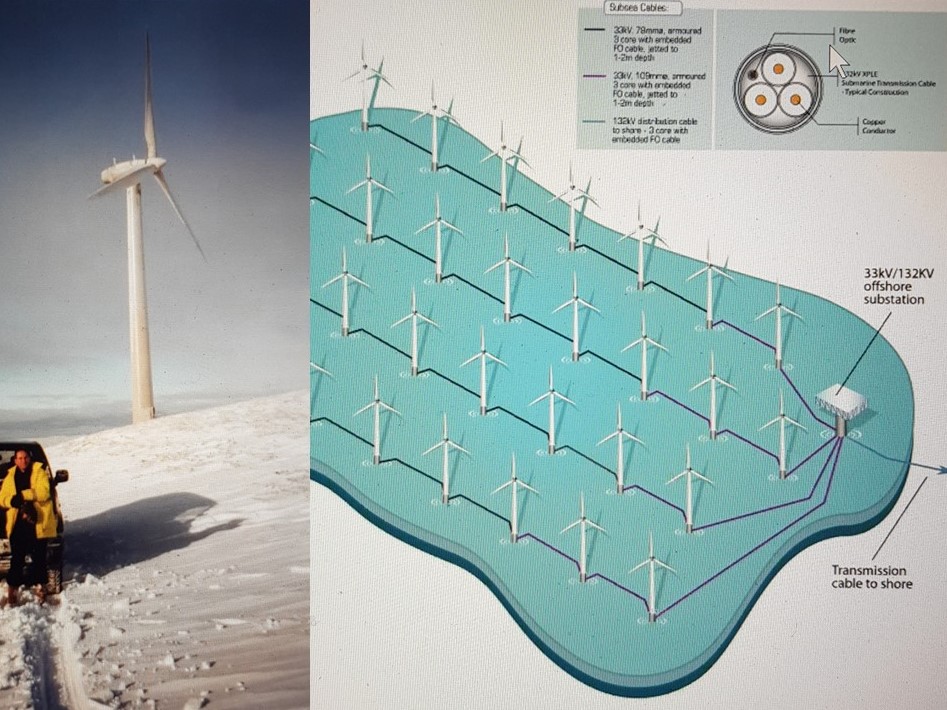
Rupert, who was introduced to us by PP Richard Kemball-Cook at the start of his presentation, started his career as an engineer with the Royal Navy before going on to become a naval architect.
He’s been involved in wind power since its early days. He built his first wind farm in 1996 – just 5 years after the first wind farm was built in the UK in Cornwall. His company (KBR) already had a large offshore presence so was in a perfect position to build the offshore wind farm off Barrow-in-Furness in the Irish Sea. They were also the first group to build an offshore substation for an offshore wind farm in the UK.
One key fact that Rupert wanted us all to take home from his talk was: “a wind farm repays the energy that it takes to build it in less than one year” adding “that includes producing the steel and doing the construction, fabrication and installation – the whole thing!” Thus, he said, wind turbines give very good “energy payback”.
He showed us an impressive video clip showing a massive turbine described as a “state of the art” turbine when it was erected in 1996. This turbine could produce 600 kilowatts and was one of 36 on that particular wind farm.
Astonishingly, that turbine was still active in 2016 – 20 years later, showing just how durable turbines are. During its years of use the turbine ran virtually without problem. Its lifespan (and that of the other turbines on the farm) has therefore been offered an extension from 20 years to 31 years.
Rupert then talked us through his slideshow, illustrating points with pictures of the magnificent structures accompanied by some impressive statistics about wind farms and their continuing development.
The Winstanley wind farm in Dumfries, for instance, was not only the highest wind farm in Europe when it was built, but it saved 50,000 tonnes of carbon dioxide from going into the air each year. The turbine only needed a tiny amount of power to work – around 21 mW in total – and the turbine itself was over 2,000 feet high. Rupert described how it had been difficulty to build because of its location…and inclement weather. (Though, ironically, when it came to be commissioned the wind fell away altogether meaning that the turbines wouldn’t turn!)
Rupert told us that a wind turbine needs around 15m/s of wind over the year to generate its full output; in reality this doesn’t happen – wind speeds can be considerably lower or higher. Based on an average home using around 400 kilowatt hours per year, we learnt that the 36 turbines on the Dumfries farm could generate enough power for over 14,000 homes.
Rupert moved on to talk about offshore wind farms. We learnt that these are more effective than those on land as wind quality is much stronger and “better” (it’s more “laminar” as it doesn’t have to blow around hills). He showed a stunning picture of the Horns Rev offshore wind farm off the coast of Denmark, taken in unusual weather that made each foot of the turbine seem to rise out of nowhere.
We learnt that turbines towards the back of a farm (downwind turbines) don’t give as much energy as those at the front due to a “wake effect” – often resulting in a drop of 20-30% of turbine power. We also learnt of the great advances that have been made in generating power using turbines.
The UK first allowed offshore wind farms to be built around 2000/1. Many companies put in bids and KBR was very successful – getting around 18 sites approved in total, with up to 30 turbines allowed at each site.
Rupert told us a little about how a wind turbine works, describing the role various parts play, and giving plenty of facts and figures along the way. (We learnt that the yaw motor, for example, turns the turbines into the wind.)
Rupert also spoke about the structure of a turbine: the huge vertical “pole” consists of two concentric tubes (a monopile and a transition tube) hammered vertically. The monopiles were around 4.75 metres in diameter while the monopile wall was around 45-80 mm thick. The structure also had a number of ladders, tubes and cables – the ladders being accessible from a boat for maintenance.
We were surprised to learn that building an offshore wind turbine requires an installation vessel – basically like a big ship! Before such vessels came into being, firms would “cobble together” pieces of oil rigs in order to position turbines in place. However, it was soon decided that custom-built turbine installation vessels would be a better option. These self-propelled vessels have their own engines and GPS, allowing them to serve as mobile “jack up” rigs in the precise position where turbines are to be erected. The MPI project was the first to use such a setup, at a cost of over 35 million dollars.
We were also told that each farm needs a laydown area where equipment and construction materials are kept. In this case, the unused Harland and Wolff shipyard in Belfast (where the Titanic was built) was used.
When putting the monopile in place (using GPS) the installation vessel is jacked up and a 1200 tonne hydraulic hammer is used to hammer the monopile into the ground. Around 28 km of cables (weight over 1,344 tonnes) run to and from the substation alongside fibre optic cables needed to control the system via a computer link. There is even a living compartment in case people get stranded!
Rupert also spoke of a more recent wind farm that has 3000 kilowatt turbines, producing enough power for over 70,000 homes!
Rupert also talked briefly about the London Array offshore wind farm at Graveny, and the Kentish Flats farm which can be seen from Whitstable. The substation was buried into the hillside so as not to be an eyesore. The farm has two offshore substations, with the power brought in by four cables (two from each substation).
Illustrating the strategic importance of wind farms, Rupert told us how permission to continue to build Triton Knoll wind farm, off the coast of Lincolnshire, was given even during lockdown.
Rupert then recounted the story of how he happened to meet some Japanese representatives of Mitsubishi Heavy Industries following a talk he gave. Six weeks later he’d been asked to give a talk on how to build an offshore wind farm – and this was followed by further questions about what turbine size might be most economical. A subsequent consultation found the answer was 7 megawatts! They then went off to build such a turbine – which actually turned out to be a 9.5 megawatt turbine. These turbines have a 164m (approx.) rotary diameter – compared to 39m at the wind farm mentioned earlier). A neat image nicely illustrated this uphill “movement” in size.
Finally, we learnt that “a few big turbines are more efficient than lots and lots of little ones”. Rupert told us that turbines continue to improve and increase in size – an even bigger,12 megawatt, wind turbine is being developed for Dogger Bank wind farm. The turbine, which has a rotary blade of more than 100m long, is being built in China at the moment. In this case the installation vessel will need a 300 tonne crane. “It’s a monster!” said Rupert.
Rupert answered some questions before Brian Dobinson gave a vote of thanks on our behalf.
Picture: Some of the pictures Rupert used during his talk.